Pra Rancangan Pabrik Asam Sulfat Dari
Sulfur, Udara Dan Air Dengan Proses DOUBLE
CONTACT PROCESS Dengan Kapasitas 300.000 Ton/Tahun
Abstrak
Jurnal
ini membahas tentang proses pembuatan asam sulfat dari sulfur udara dan oksigen
dengan proses double contact kapasitas 300.000 ton/tahun. Produksi asam sulfat
memiliki prospek yang baik untuk dikembangkan, karena bahan baku yang digunakan
sangat mudah didapat dan murah. Keunggulan dari proses ini adalah kemurnian
produk yang dihasilkan sebesar 99,5%. Dari hasil analisi ekonomi, Percent
Return Of Investment (ROI) 15%, Pay Out Time (POT) 4,2 Tahun, Break Even Point
(BEP) 43,06 %. Ditinjau dari segi ekonomi, pabrik asam sulfat dengan kapasitas
300.000 ton/tahun ini layak untuk didirikan.
Abstract
This
journal discusses the process of making sulfuric acid from air sulfur and
oxygen with a double contact process with a capacity of 300,000 tons / year.
The production of sulfuric acid has a good prospect to be developed, because
the raw materials used are very easy to obtain and inexpensive. The advantage
of this process is that the purity of the product is 99.5%. From the results of
economic analysis, Percent Return of Investment (ROI) is 15%, Pay Out Time
(POT) is 4.2 years, Break Even Point (BEP) is 43.06%. In terms of the economy,
this sulfuric acid plant with a capacity of 300,000 tons / year is feasible to
be established.
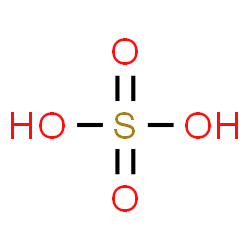
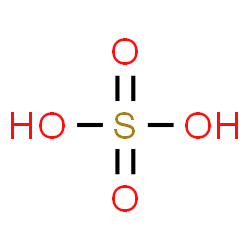
1.1
Latar Belakang Pendirian Pabrik
Asam Sulfat merupakan
salah satu bahan kimia yang penting dan dibutuhkan di sebagian besar dunia
industri. Terutama pada industri pupuk Ammonium sulfat yang bahan bakunya
merupakan ammonia dan Asam sulfat (Mangundap, 2013). Selain itu Asam sulfat
juga dibutuhkan oleh banyak industri lainnya seperti industri Natrium sulfat,
industri Alumunium sulfat, industri Natrium bisulfit dan industri Dimetil
sulfat.
Adapun industri logam
membutuhkan Asam sulfat untuk proses pickling yaitu proses untuk menghilangkan
karat yang melekat pada permukaan logam. Seiring bertambahnya kebutuhan akan
produk-produk tersebut maka kebutuhan Asam sulfat juga ikut meningkat. Meskipun
di Indonesia sudah ada industri yang memproduksi Asam sulfat dengan total
produksi ± 1 juta ton/tahun, akan tetapi belum dapat mencukupi kebutuhan dalam
negeri, sehingga Indonesia masih membutuhkan Asam sulfat dari luar negeri.
Pada umumnya sebagian industri
yang membutuhkan Asam sulfat, memiliki unit untuk pengolahan Asam sulfat sendiri, agar mengurangi biaya pembelian
bahan baku. Oleh karena itu pabrik ini dirancang untuk memenuhi kebutuhan Asam sulfat
dalam negeri, khususnya industri logam.

Beberapa manfaat asam sulfat
diantaranya adalah
A. Banyak di gunakan di berbagai
industri sebagai bahan baku diantaranya bahan
baku:
·
Pupuk ZA
·
Industri
kertas,kaca dan sabun
·
Penjernihan
air
·
Pabrik
kertas
·
Bahan
Pemutih
·
Bahan
Pengawet makanan
·
Industry
detergen
·
Bahan aktif
pestisida
·
Carbonat
·
Formulasi
pestisida
B. Asam sulfat sangat dibutuhkan untuk
proses pickling pada industri baja.
2.
Macam – macam Proses
Pada dasarnya semua
produksi asam sulfat menggunakan metode yang sama, yaitu konversi gas SO2
menjadi gas SO3 secara katalitik, mereaksikan gas SO3 dan
H2O menjadi asam sulfat, dan melanjutkannya dengan proses kontak Gas
SO3 dengan asam sulfat yang diencerkan. Berdasarkan sumber gas SO2
berasal, produksi asam sulfat secara komersial dibedakan menjadi Single Contact
Process, Double Contact Process, Wet Contact Process, Pressure process dan H2O2 Process
(Ashar, 2013).
2.1
Single Contact Process (single Absorption)
Proses ini digunakan
untuk kadar SO2 yang rendah ketika akan masuk kedalam konverter,
umumnya gas umpan masuk konverter berasal dari proses industri lain yang mengandung SO2 sekitar 3-10%
berdasarkan volume (Nieuwenhuyse, 2000). Gas yang mengandung SO2
tersebut dioksidasi secara katalitik menjadi SO3, yang kemudian
dialirkan menuju proses kontak di absorber, dalam proses ini hanya melewati
satu tahap proses kontak. Konversi untuk proses ini mencapai 98.5%, akan tetapi
dibeberapa industri untuk mencapai konversi lebih dari 98% merupakan hal yang
sulit.
2.2 Double Contact Process (Double
Absorption)
Pada proses ini konversi yang dihasilkan
dapat mencapai 99.5%, konversi tersebut dapat dicapai dengan mengalirkan gas SO3
yang terbentuk di konverter tahap pertama, menuju absorber pertama(Intermediate
Absorber) untuk dipertemukan dengan asam sulfat yang diencerkan, jika
diperlukan, gas SO3 tersebut dialirkan kedalam Oleum Absorber
terlebih dahulu. Untuk memperoleh konversi yang lebih tinggi gas SO2
yang masih terbawa didalam absorber pertama dialirkan kembali menuju konverter
tahap kedua, gas SO3 yang terbentuk di konverter tahap kedua
dialirkan menuju Absorber kedua untuk dipertemukan kembali dengan asam sulfat
yang diencerkan. Pada umumnya gas umpan masuk kedalam konverter mengandung SO2
mencapai 12 % berdasarkan Volumenya (Nieuwenhuyse, 2000).
|
2.3 Wet Contact Process
Berbeda dengan
kontak proses yang lainnya, Wet Contact Process menggunakan umpan yang masih
mengandung kadar air ketika masuk kedalam konverter. Umumnya, sulfur trioksida
(SO3) yang terbentuk karena oksidasi katalitik SO2,
bereaksi dengan kadar air yang terbawa oleh umpan membentuk asam sulfat berfasa
uap, yang kemudian di kondensasikan menjadi fasa cairnya (Almirall, 2009).
Didalam sebuah kondisi SO3 yang terbentuk didinginkan dan secara
langsung dialirkan ke kolom absorpsi untuk
membentuk asam sulfat.biasanya proses ini digunakan ketika sumber SO2
yang digunakan berasal dari hasil pembakaran H2S. Jumlah SO2 yang
masuk ke dalam Konverter umumnya 0.05-7% volume. Konversi yang didapat dari
proses ini mencapai 98%.
2. Tahapan
Pembentukan Asam Sulfat
·
Air (H20)
Bahan baku
yang diperlukan yaitu air, yang diperoleh dari waduk Krakatau Steel.
·
Sulfur (S)
Sulfur
diperoleh dari tambang sulfur di Tangkuban perahu berupa padatan dan disimpan
dalam Silo ,setelah sebelumnya sulfur dihaluskan dengan menggunakan Ball Mill.
·
Udara
Udara yang
digunakan berasal dari lingkungan sekitar, digunakan sebagai pendingin terlebih
dahulu sebelum memasuki Furnace tanpa memerlukan proses pengeringan terlebih
dahulu.

Sulfur udara sulfurdioksida
Bubuk
Sulfur berasal dari Silo 1 (S-01) dan dimasukkan ke dalam Furnance dengan menggunakan Bucket Elevator, dan
dibakar dengan menggunakan udara panas berlebih. Suhu hasil pembakaran,
mencapai 1000oC. Panas tersebut digunakan untuk membangkitkan steam
pada waste heat boiler di dalam Furnance tersebut, sehingga suhu yang keluar
dari Furnance sebesar 427oC.
B. Pembentukan
SO3
SO2 +
½ O2 → SO3
sulfurdioksida oksigen sulfurtrioksida
Mekanisme
reaksi yang terjadi pada pembentukan SO3 membutuhkan bantuan dari
katalis, secara komersial reaksi oksidasi SO2 menjadi SO3 menggunakan
katalis yang mengandung 4-9 % berat V2O5 (Vanadium Pentoxide), sebagai komponen
aktif, dan dicampur dengan logam alkali sulfat sebagai promotor. Dibawah
kondisi operasi, katalis ini akan meleleh ketika reaksi berlangsung. Biasanya Potassium Sulphate digunakan sebagai
promotor akan tetapi pada akhir-akhir ini Caesium
Sulphate sudah mulai digunakan karena titik lelehnya yang rendah, yang
menandakan katalis dapat digunakan pada temperatur yang lebih rendah.
Untuk
promotor katalis yang komersial, batasan temperatur pada katalis untuk memulai
reaksi yaitu 410-430oC. Sedangkan 380-390oC untuk Caesium Sulphate. Batasan temperatur
maksimal katalis yaitu 650oC. Melebihi temperatur tersebut maka
katalis akan kehilangan tenaga katalitiknya secara permanen. Oleh karena itu
proses oksidasi SO2 menjadi SO3 dilakukan pada temperatur
sekitar 400-650oC.
Konverter
R-01 merupakan reaktor jenis fix bed, dirancang sehingga memiliki 4 bed yang
terpisah dan dibagi menjadi 2 tahap. Tahap pertama, reaksi oksidasi SO2
dikonversi menjadi SO3 terjadi dengan mengalirkan aliran gas
mengandung SO2 melalui 3 bed pertama, dimana masing-masing bed
mengandung katalis Vanadium. konversi yang terjadi terhadap SO2
menjadi SO3 pada 3 Bed pertama mencapai 98%. Setelah melalui 3 tahap
pertama, aliran gas yang mengandung gas SO3, didinginkan dan
dialirkan menuju Packed Tower 1(PT-01) untuk menyerap gas SO3 menggunakan
larutan H2SO4. Gas yang keluar dari PT-01, masih
mengandung gas SO2 yang belum terkonversi sehingga aliran gas
tersebut dialirkan kembali ke dalam Bed 4, konversi total mencapai 99.5%.
C.
Absorbsi SO3 oleh
H2SO4 Pekat
Gas yang mengandung SO3 kemudian dialirkan ke
Packed Tower untuk diabsorbsi menggunakan H2SO4 98%. Asam Sulfate pekat yang telah menyerap
gas SO3 berubah kenampakan nya menjadi Asam Sulfate Berasap (H2S2O7)
yang biasa dikenal dengan Oleum.
Reaksi : H2SO4 + SO3 → H2S2O7
Asam Sulfat sulfurtrioxsida oleum
3.1.3
Tahapan pemurnian
dan pembentukan produk
A. Pembentukan
Asam Sulfat Pekat
Oleum dari packed tower kemudian dialirkan menuju Washing
Tank untuk di tambahkan dengan air sehingga Oleum
terkonversi kembali menjadi asam sulfat
Reaksi : H2S2O7 +H2O →2 H2SO4
oleum air
asam sulfat
B. Pemurnian
Produk Asam Sulfat
Larutan asam sulfat hasil washing, sebagian dialirkan
menuju mixing untuk menambahkan air sehingga konsentrasi asam sulfat menjadi
98% dan digunakan kembali sebagai absorben SO3 di Packed Tower.
Sedang sebagian lagi dialirkan ke tangki penyimpanan sebagai produk untuk
dipasarkan.
3. Kesimpulan
Berdasarkan
tinjauan kondisi operasi, pengadaan bahan baku, dan keberadaan pabrik sejenis,
maka pabrik asam sulfat tergolong pabrik beresiko sedang.
Hasil
analisis ekonomi pabrik ini menunjukkan:
1.
Proses
pembuatan Asam Sulfat dengan bahan baku sulfur, udara dan air dengan menggunakan
proses DOUBLE CONTACT PROCESS dengan kapasitas 300.000 Ton/Tahun.
2.
Pabrik ini
direncanakan didirikan pada tahun 2021 dan mulai beroperasi di tahun 2020 di
Cilegon Banten. Bahan baku Sulfur diperoleh dari tambang di tangkuban perahu.
3.
Percent
Return of investment (ROI) 15%.
4.
Pay out
time (POT) 4,2 tahun.
5.
Break event
point (BEP) sebesar 43,06%.
Hasil analisa ekonomi
diatas menunjukkan bahwa pabrik asam sulfat dari sulfur,udara dan air dengan
proses DOUBLE CONTACT PROCESS dengan
kapasitas 300.000ton/tahun layak untuk didirikan.
DAFTAR
PUSTAKA
Anonim.
Equip Costs. Home page on-line. Available from :
Anonim.
Konsumsi Sulphuric Acid. Home page on-line. Available from:
Anonim.
Konsumsi Sulphuric Acid. Home page on-line. Available from :
Anonim.
Konsumsi Sulphuric Acid. Home page on-line. Available from :
Banchero,
Julius T. 1987. Introduction to Chemical Engineering. Singapore.
McGraw-Hill Inc.
Branan,
Carl. 2005. Rules of Thumb Chemical Engineers. United States. Elsevier
Inc.
Brownell,
L.E., and Young, E.H. 1959. Process Equipment Design. New York:
John Wiley and Sons Inc.
Brown, G.G.
1978. Unit Operation. Modern Asia Edition. New York: John Wiley
And Sons Inc.
Christensen
A Kurt. 2011. Process For The Production Of Sulphuric Acid.
United State Patent.
Christensen
A Kurt. 2011. Meeting Future SO2 Emission Challenges With
Topsoe’s New VK-701 LEAPS5 Sulphuric
Acid Catalyst. Denmark.
Cloulson
and Richardson’s. 2005. Chemical Engineering Design New York: John
Wiley and Sons Inc.
Davenport,
W.G. King. M J. Rogers, B Weissenberger, A. 2006. Sulphuric Acid
Manufacture. South African Institute
of Mining and Metallurgy
Johannesburg.
Dow.
2005. Heat Transfer Fluids Chemical Company, United States. Canada.
Dorr
Heinz, K. Et al. 1983.Process of Producing Concentrated Sulphuric Acid.
US Patent Documents.
Kern,
D.Q. 1982. Process Heat Transfer. New York : Mc Graw Hill.
Louis
N. Allen, Jr. 1953. Sulphuric Acid Produstion By Absorption.
US Patent Documents.
Mc
Cabe, W.L, Smith, J.C. and Harriot, P. 1985. Unit Operation of Chemical
Engineering. 5Th Edition. Singapore:
Mc Graw Hill Book Co.
Nieuwenhusye
Van, E.A. 2000. Production of Sulphuric Acid. European Fertilizer
Manufacturers Association. Belgium.
Perry,
R.H. and Green, D. 1999. Chemical Engineering Handbook. ED. 7 . New
York: Mc Graw Hill.
Peters,
M.S. and Timmerhause, K.D. 1991. Plant Design and Economics for
Chemical Engineering. Ed 7.
Singapore: McGraw Hill.
Sinnott,
R.K. 2005. Chemical Engineering Design. ed 4.
Schillmoller,
C.M. 2014. Selection And Performance of Stainless Steels and Other
Nickel-Bearing Alloys in Sulphuric
Acid. Nickel Development Institute.
Seitz
Ekkehart. Et al. Method of Manufacturing Sulphuric Acid. United State
Patent.
Smith
J.M. and Van Ness, H. C. 1996.
Introduction to Chemical Engineering
Thermodynamics. Ed 5. Singapore:
McGraw Hill International Edition.
Treybal,
R.E. 1968. Mass Transfer Operation. 3rd edition. New York: McGraw
Hill Book co.
Walas,
S.M. 1988. Chemical Process Equipment. America: Butteerworths.
Yaws,
L. Carl. 1998. Chemical Properties Handbook. London: McGraw Hill.
- Eka Widyaningsih
- Madinah Fitri
*Ilmu tanpa amal, bagaikan pohon tanpa Buah.. maka berbagilah.. 😊